Acrylic, a versatile and widely used material, has become an integral part of modern manufacturing. Known for its durability, clarity, and ease of molding, acrylic is used in a variety of industries, from automotive and construction to design, healthcare, and electronics. As technology evolves, the process of acrylic manufacturing is undergoing significant transformations, moving toward smarter, more efficient, and automated production methods. The future of acrylic manufacturing is set to be shaped by the integration of smart technologies, which promise to enhance quality, reduce waste, and streamline production.

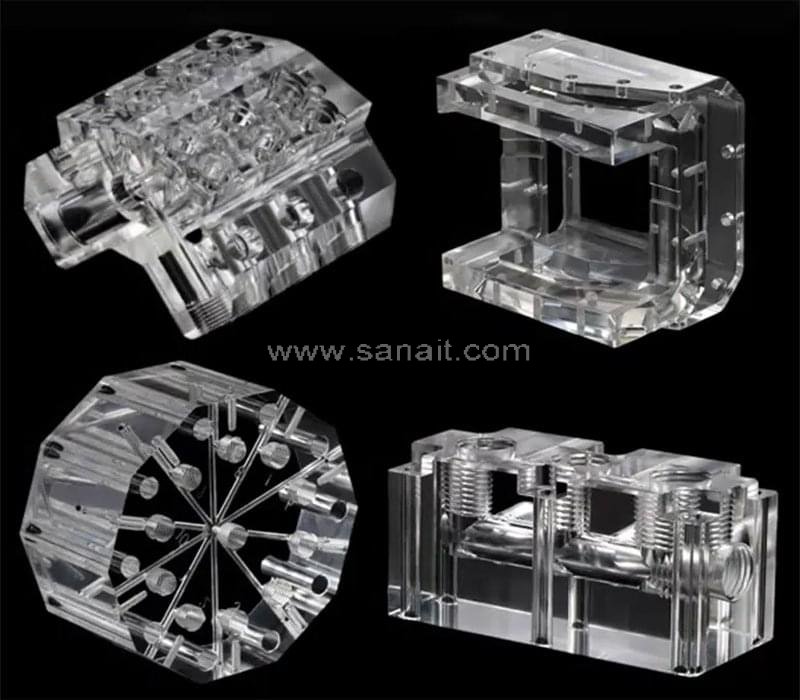
The Current Landscape of Acrylic Manufacturing
Traditional acrylic manufacturing involves a series of complex steps, including extrusion, casting, and thermoforming, to create products like sheets, tubes, and molds. These processes have been optimized over the years, but challenges still persist. Energy consumption, material waste, and the need for skilled labor remain persistent concerns within the industry. As consumer demands continue to increase for faster production times, lower costs, and higher-quality products, manufacturers are increasingly turning to smart technologies to address these challenges.
The Role of Smart Manufacturing Technologies
Smart manufacturing refers to the integration of advanced technologies such as the Internet of Things (IoT), artificial intelligence (AI), robotics, and data analytics to optimize production processes. These technologies have already begun to make their way into the acrylic manufacturing industry, and their role is expected to grow exponentially in the coming years.
- Automation and Robotics: The introduction of robotic systems to acrylic production lines is revolutionizing the industry. Robots can perform tasks such as cutting, shaping, and assembling acrylic products with precision and consistency, significantly reducing human error. These robots can also work continuously, optimizing production efficiency and cutting down on labor costs. Automation also makes it possible to scale production without compromising quality.
- Internet of Things (IoT): IoT technologies are enabling manufacturers to monitor and control their production lines in real-time. Sensors embedded in machines can track temperature, pressure, and material flow, ensuring that each step of the manufacturing process is within optimal parameters. This real-time data collection helps identify potential issues before they escalate into major problems, reducing downtime and improving overall production efficiency.
- Artificial Intelligence (AI) and Machine Learning: AI and machine learning algorithms can be used to analyze production data and predict future trends. These technologies allow for predictive maintenance, which ensures that equipment is serviced before failures occur, reducing unplanned downtime. AI can also assist in process optimization by analyzing vast amounts of data and recommending adjustments to improve product quality and reduce waste.
- 3D Printing and Customization: With the advent of 3D printing, manufacturers can now create complex acrylic structures and prototypes with high precision and speed. This technology allows for the production of customized acrylic products on demand, catering to specific customer needs without the need for large production runs. 3D printing also eliminates the need for molds, reducing material waste and lead time.
- Advanced Materials and Sustainable Practices: In addition to improving manufacturing processes, smart technologies are also pushing the boundaries of material innovation. New materials and processes are being developed that reduce the environmental impact of acrylic production. For example, bio-based acrylics made from renewable resources are being explored as a sustainable alternative to traditional petroleum-based acrylics. Smart manufacturing practices also aim to reduce energy consumption and material waste, aligning with global efforts toward sustainability.
The Benefits of Smart Acrylic Manufacturing
The integration of smart technologies into acrylic manufacturing offers a range of benefits for both manufacturers and consumers:
- Increased Efficiency: Automation and IoT technologies streamline production processes, reducing human intervention and minimizing the likelihood of errors. Real-time monitoring allows manufacturers to make data-driven decisions that optimize the production flow, reducing lead times and boosting overall efficiency.
- Improved Quality Control: With the help of AI and real-time data analysis, manufacturers can ensure that each acrylic product meets the highest standards. Automated inspection systems can detect defects early in the production process, reducing the number of flawed products that reach the market.
- Customization and Flexibility: 3D printing and advanced digital technologies enable greater product customization. Manufacturers can quickly adapt to changing customer preferences and market trends by offering bespoke acrylic products that meet specific needs.
- Cost Reduction: By automating processes, optimizing production, and reducing waste, smart manufacturing technologies contribute to cost savings. Predictive maintenance and the use of renewable materials also help reduce long-term operational costs.
- Sustainability: With growing concerns over environmental impact, the adoption of sustainable practices in acrylic manufacturing is becoming a priority. The shift towards bio-based materials and energy-efficient processes aligns with global sustainability goals and helps reduce the carbon footprint of the industry.
Challenges and the Path Ahead
Despite the promising future of smart acrylic manufacturing, challenges remain. The initial investment in smart technologies can be high, particularly for smaller manufacturers. Additionally, there is a need for skilled workers who can operate and maintain these advanced systems. Training and upskilling the workforce will be crucial to the success of this technological transition.
Moreover, as with any industry, there are concerns about data security and the potential for cyberattacks. As IoT and AI systems become more integrated into manufacturing, ensuring the security of production data will be critical.
However, these challenges are not insurmountable. As the cost of smart technologies continues to decrease and the benefits become more evident, the transition toward smart acrylic manufacturing will gain momentum. Collaboration between manufacturers, technology providers, and policymakers will be essential to addressing these challenges and ensuring the successful integration of smart technologies into the acrylic manufacturing sector.
Conclusion
The future of acrylic manufacturing is bright, thanks to the rapid advancements in smart technologies. By incorporating automation, AI, IoT, 3D printing, and sustainable practices, manufacturers can achieve greater efficiency, improve product quality, and reduce environmental impact. While there are challenges to overcome, the potential for a smarter, more sustainable acrylic manufacturing industry is within reach. As the industry evolves, we can expect to see a new era of production that is faster, more flexible, and more sustainable—shaping the future of acrylic manufacturing for years to come.